Publication Date
3-1-2021
Document Type
Article
Publication Title
Sensors
Volume
21
Issue
5
DOI
10.3390/s21051654
First Page
1
Last Page
18
Abstract
Current maintenance intervals of mechanical systems are scheduled a priori based on the life of the system, resulting in expensive maintenance scheduling, and often undermining the safety of passengers. Going forward, the actual usage of a vehicle will be used to predict stresses in its structure, and therefore, to define a specific maintenance scheduling. Machine learning (ML) algorithms can be used to map a reduced set of data coming from real-time measurements of a structure into a detailed/high-fidelity finite element analysis (FEA) model of the same system. As a result, the FEA-based ML approach will directly estimate the stress distribution over the entire system during operations, thus improving the ability to define ad-hoc, safe, and efficient maintenance procedures. The paper initially presents a review of the current state-of-the-art of ML methods applied to finite elements. A surrogate finite element approach based on ML algorithms is also proposed to estimate the time-varying response of a one-dimensional beam. Several ML regression models, such as decision trees and artificial neural networks, have been developed, and their performance is compared for direct estimation of the stress distribution over a beam structure. The surrogate finite element models based on ML algorithms are able to estimate the response of the beam accurately, with artificial neural networks providing more accurate results.
Keywords
Artificial neural networks, Beam analysis, Finite element, Gradient boosting regression trees, Machine learning, Random forest trees, Structural monitoring
Creative Commons License
This work is licensed under a Creative Commons Attribution 4.0 License.
Department
Aerospace Engineering; Aviation and Technology
Recommended Citation
Poojitha Vurtur Badarinath, Maria Chierichetti, and Fatemeh Davoudi Kakhki. "A machine learning approach as a surrogate for a finite element analysis: Status of research and application to one dimensional systems" Sensors (2021): 1-18. https://doi.org/10.3390/s21051654
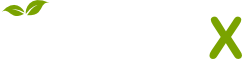
- Citations
- Citation Indexes: 60
- Usage
- Downloads: 62
- Abstract Views: 24
- Captures
- Readers: 158
- Mentions
- Blog Mentions: 1